Solar Panel Cleaning Safety Consulting

Carla Dawson
June 15, 2023Solar Panel Cleaning Safety Considerations
Solar Energy is growing and with this comes the need for solar panel cleaning. However, this industry is in its infancy and safety is not top of mind for many service providers yet it should be. Solar panel cleaning adds a new component of risk that is not typically found in other surface cleaning industries and this risk is electrical. Junction boxes and DC connectors are one of the many areas of risks a solar panel cleaner should be aware of. Understanding the basic risks in solar panel cleaning is critical and then learning how to mitigate them
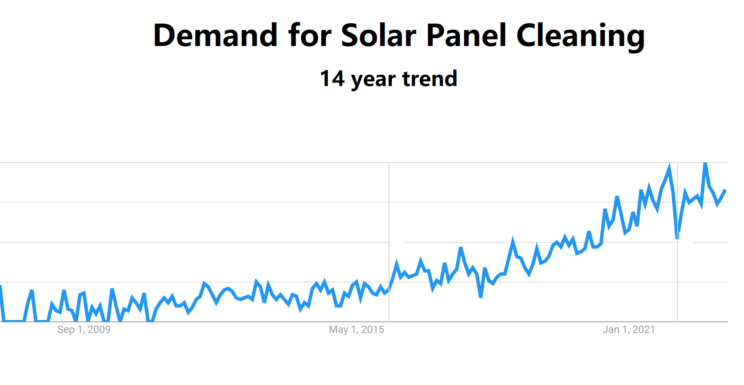
Solar Panel Cleaning Safety Starts in the Design Phase of a Solar Installation
Solar is growing at double-digit rates worldwide and this trend is likely to continue for at least another 25 years. Solar panel cleaning safety can be contemplated and designed for during the design phase. The challenge is that PV designers have been trained to only focus on performance without thinking about the risks for solar panel cleaners. Safe solar panel cleaning can be accomplished by 1) Designing with safety in mind and 2) Constant training and creating a company culture of safety. Safe Centric company culture.
To help the industry manage safety risks, Soilar Tech has created a short list of topics just to get started. The content can be found within our courses that also get you NABCEP credits. https://school.soilar.tech/
Introduction to Solar Panel Cleaning Safety
Job Hazard Analysis
Solar Cleaning Hazards
Solar Cleaning Hazards
Fall Protection
Conclusion
How can solar panel cleaning be included in the design phase of a solar installation?
Solar Panel Cleaning Safety Consulting starts in the design phase but is also needed during Operations and Maintenance

Solar Panel installation types vary significantly and each one has its own unique safety risks. Accessibility is one of the challenging aspects of solar panel cleaning and especially in the rooftop and floating segments. However what about the electrical risks? Solar panel cleaners rarely turn off a system to clean and water is a conductor. DC connectors are often loose, inaccurately installed or corroded.
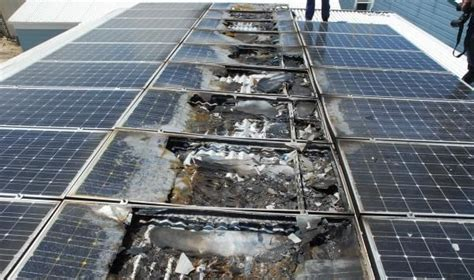
Source – https://www.slocable.com.cn/news/the-consequences-of-ignoring-the-quality-of-solar-mc4-connectors-are-disastrous
With the continuous development of the internal photovoltaic market, the demand for PV junction boxes connectors continues to grow. However, because of the low-cost ratio and the “inconspicuous” function, the quality of junction boxes and connectors has been replaced, resulting in frequent failures and accidents of solar photovoltaic power generation and systems. The problems with connectors have gradually revealed, so buyers and manufacturers have begun to realize the importance of product quality. Accidents caused by junction boxes and connectors account for more than 30%, and junction box diode breakdown accounts for more than even 65% of junction box and connector accidents. Cheng Ziyu, head of TÜV Rheinland Shanghai’s solar component smart junction box business, said that while everyone is focusing on hotspots such as battery technology and module conversion efficiency improvements, they often overlook some small but indispensable solar energy components. Components, resulting in good battery technology and good components can not be used optimally, and even cause harm during use.
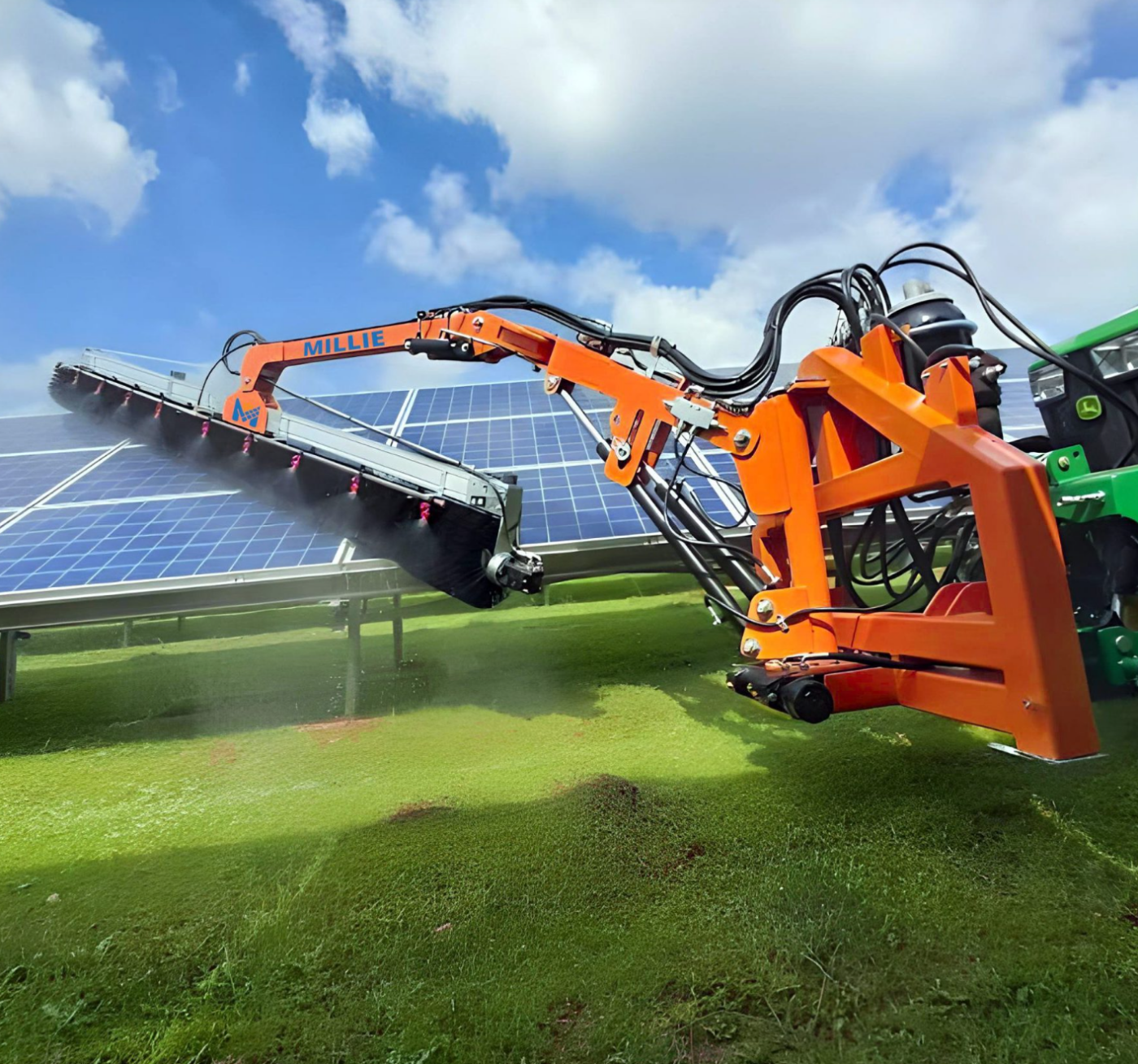
According to Dr. Zhimin Ling: “In a traditional string system, modules are arranged in series in an array with a DC high voltage of 600V-1000V. The system runs for many years, and the wire insulation is exposed after corrosion, which is very easy to generate DC arcs and cause fires. When a fire occurs, on the DC side, as long as there is light, there will be high voltage, and firefighters cannot directly put out the fire.”
Connector mixed insertion——the invisible killer of photovoltaic power station safety
Mutual insertion of connectors between different brands is also a very serious problem in the application of photovoltaic connectors. According to a foreign research report, mixed connector insertion and irregular connector installation ranked the first and third causes of fire.
There is always a problem in the photovoltaic connector market, that is, the mixed use of various connector products and the inter-plugging of connectors between different brands. This phenomenon is common in the domestic and overseas markets. Most owners and EPC companies know little about the matching of connectors.
“Connectors from different manufacturers have very different manufacturing processes, production standards, and raw materials. Related problems caused by the mutual insertion of the connectors include increased contact resistance, heat generation of the connector, fire on the connector, burnout of the connector, power failure of the string components, failure of the junction box, and leakage of the components, which may cause the system to fail to operate normally. The economic benefits of the power station are thus compromised. If products from the same manufacturer are used, this risk will be controlled within a controllable range. “
An Chao, the business manager of photovoltaic power plants and systems for TÜV Rheinland Solar Services, emphasized that solar connectors need to pay attention to compatibility issues. This issue has been raised by third-party testing agencies for many years. Therefore, connectors must not be mixed during the installation of photovoltaic power plants. In this regard, the authoritative testing organizations TUV and UL have both issued written statements that they do not support mixed insertion applications of connectors of different brands. In Australia, the government has written the requirements for power station construction to use connectors from the same manufacturer in the regulations to avoid risks. But in our country, no relevant standards have been issued in the industry.

Follow us on Instagram, Linkedin, Twitter.
Copyright © 2019 Carla Dawson. All rights reserved.
All documents are protected within the meaning of copyright law.
Carla Dawson reserves all rights to exercise intellectual property rights.
Copying of this content is not permitted without express written authority.
Violations are an offense and are liable for damages.
About the author

Carla Dawson founded Soilar Technologies, a NextGen PV Soiling Mitigation Technology Company in 2019.
NextGen PV soiling mitigation can be defined as:
“Mitigating photovoltaic soiling by using 21st-century technologies throughout the solar plant lifecycle with the objective of increasing performance, reliability, asset life, and warranty compliance. NextGen PV Soiling mitigation is typically a data-enriched smart system that combines technologies such as solar panel cleaning robotics, PV anti-soiling coatings, PV abrasion testing, bird deterrent solutions, PV soil monitoring, electrodynamic shields (EDS), condensation prevention, tracker/stowage position, and cleaning schedule optimization, solar panel cleaning software, analytics and other technologies.”
NextGen PV soiling mitigation is a phrase that was coined by Carla Dawson and Klemens Ilse in 2022.
Soilar Technologies is dedicated to helping solar panel cleaners, EPC, solar installation companies, and entrepreneurs solve their PV soiling problems from design to the operations and maintenance stage.