Best Ceramic Coatings for Solar Panels

Carla Dawson
November 1, 2023Ceramic coatings have shown their value in many fields such as the automotive industry but, the application of this technology to the “PV soiling problem” is relatively new and in development. Can ceramic coatings solve the “PV soiling problem” and if so, how and are they better than standard cleaning with water and brush systems? Does the application of ceramic coatings on solar panels always bring value or is there a time a place for this technology? What types of ceramic coatings are successful in the field of solar panels?
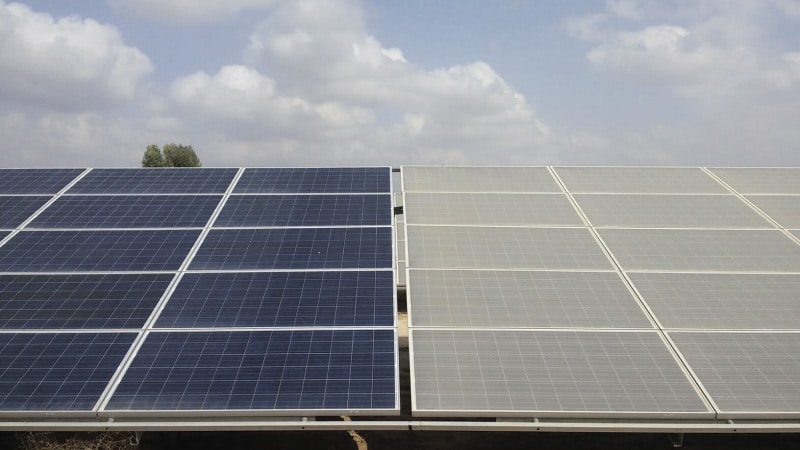
Understanding the Problem
Our research starts with having a profound understanding of the problem and asking the right questions. For example, is the glass on solar panels the same as the glass on windows? Is cleaning solar panels in the desert the same as cleaning solar panels in an area where it rains frequently? Is all PV soiling the same and does the type of soiling have an impact?
- Is the glass on solar panels the same as the glass used in standard windows? NO – Soilar.tech
- What is the difference between solar panel glass and standard glass? 97% of the glass used on solar panels is coated with anti-reflective coatings. These coatings are not used in standard windows and they are used in solar panels because they add a 3-4% energy boost. Soilar.tech
- Can anti-reflective coatings be damaged by frequent cleanings or brushes with high abrasion levels? Yes – Soilar.tech
- Are all ceramic coatings the same? No. Ceramic coatings vary significantly and the application of different coatings in the same experiment will bring different results. – Soilar.tech
- How do ceramic coatings for solar panels vary? Ceramic coatings are divided into 2 main groups. 1) Hydrophilic and Hydrophobic. Learn more in our video here. https://youtu.be/c4Enp3RW9AI
- Do all nanotechnology coatings have ceramic properties? – No Soilar.tech
PV Soiling Management 101
Before we jump into coatings for solar panels, some key concepts must be reviewed.
AntiReflective Coating For Solar Panels
Here are some visuals to help understand the problem a bit more. On the left-hand side, we can see a piece of glass that is not coated with anti-reflective coatings. On the right, the glass is coated with anti-reflective coatings. The coating of the panels adds a 3-4% energy boost which generally translates into a 3-4% revenue boost.
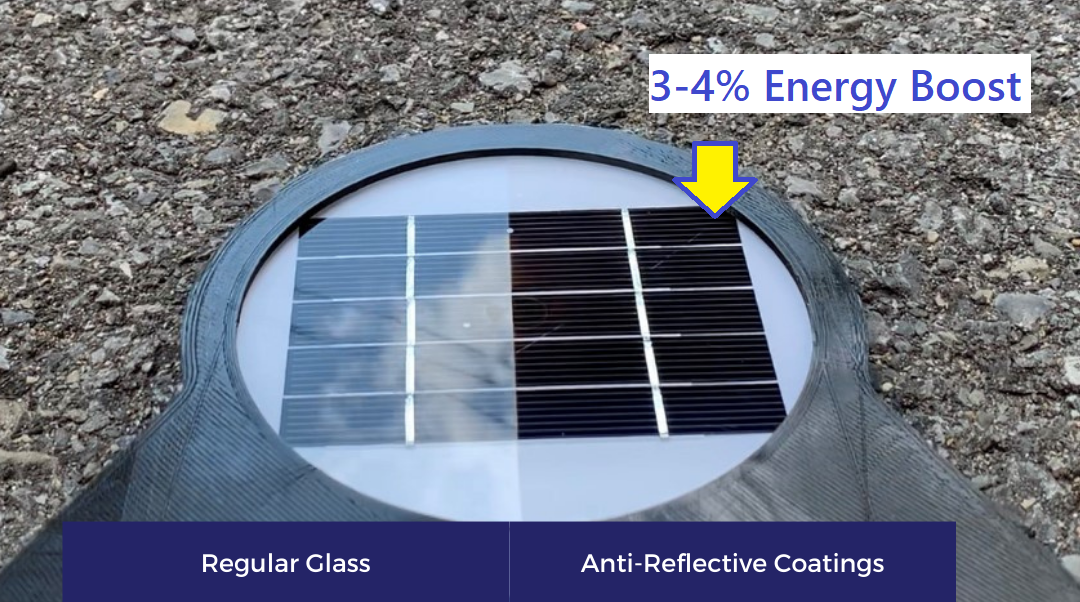
Brush Abrasion can Damage Anti-Reflective Coatings
This scanning electron microscope (SEM) image of a porous SiO2 AR coating on a typical PV module after about 6 years in a solar utility is a stark reminder of the damage that cleaning can cause to solar panels.
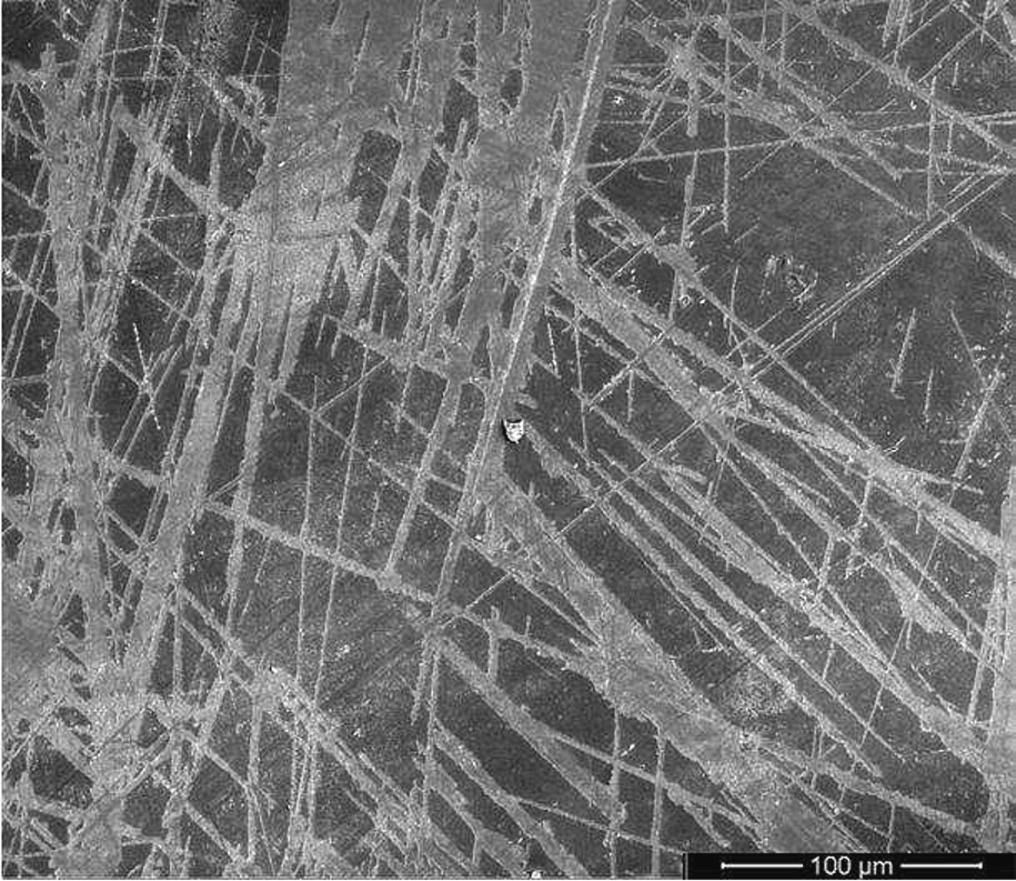
Average Daily PV Soiling Levels Around the World
Site-specific PV soiling levels should always be used to determine optimum solutions however below, I am including average daily PV soiling levels by region to help communicate a point. Notice that daily soiling levels are much lower than the value added by antireflective coatings. To solve a 1% problem we can create a 4% problem by damaging the anti-reflective coatings on solar panels. However, not all brushes degrade anti-reflective coatings, yet many of them do.
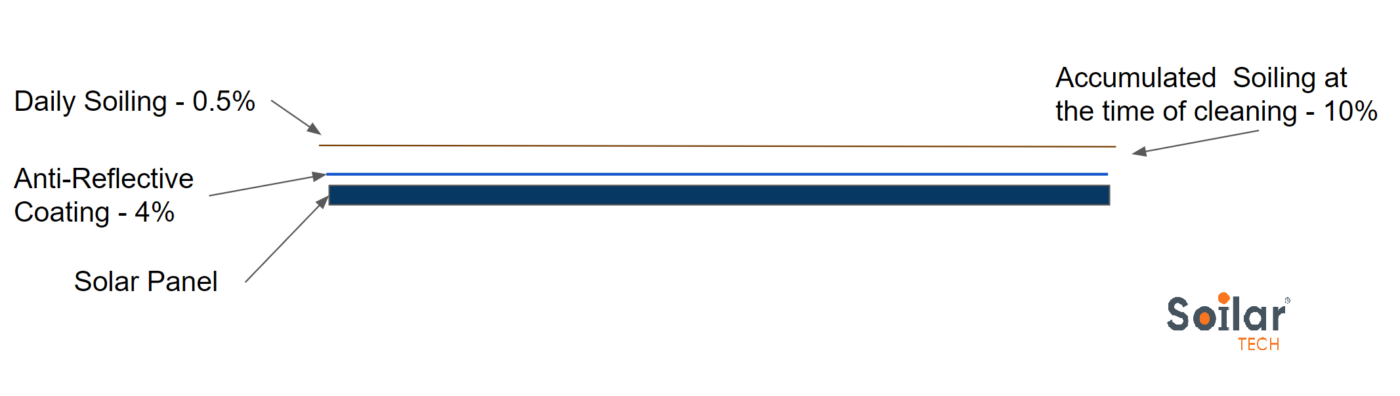
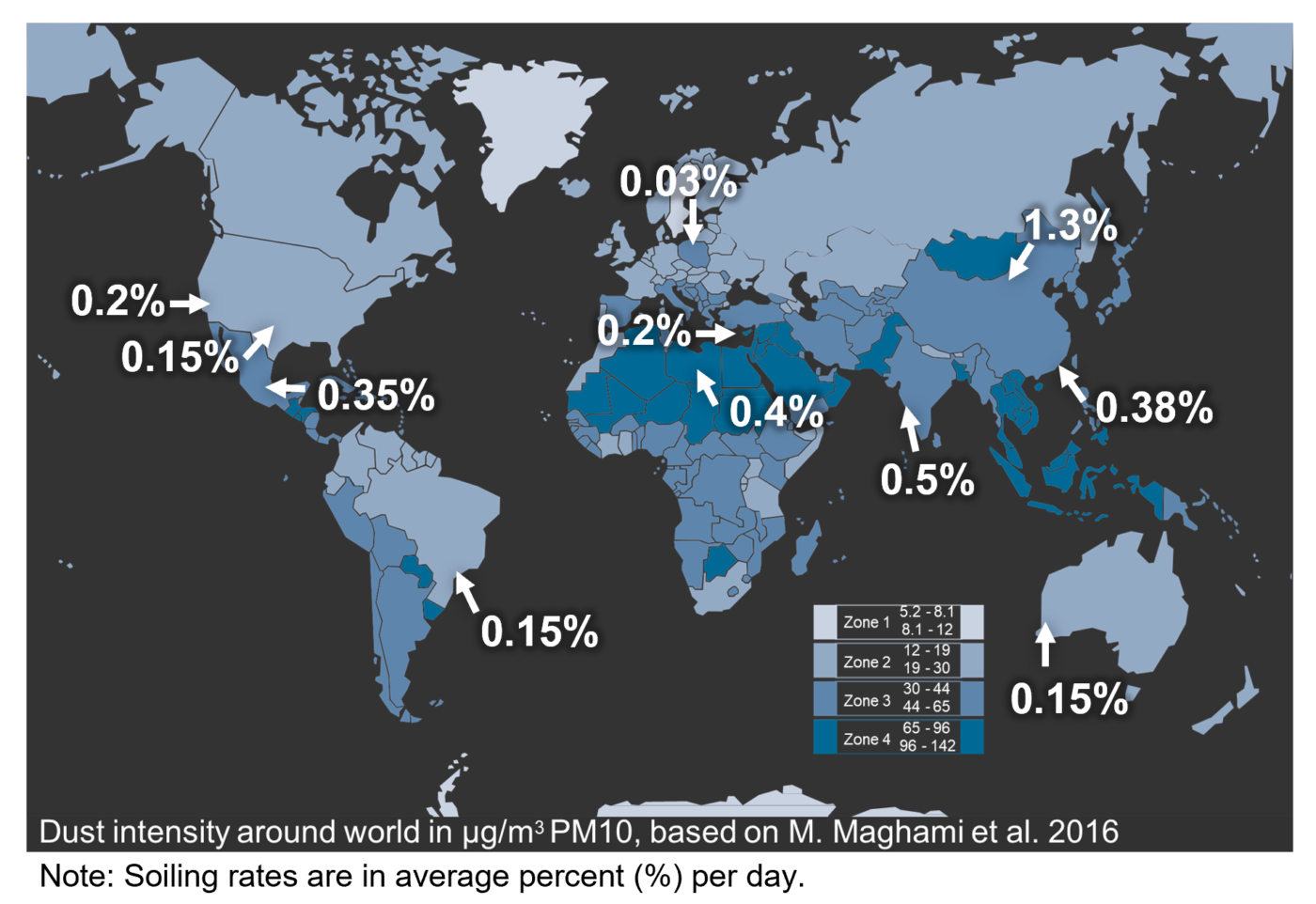
PV Soiling is Site Specific
A common statement on the internet states that PV soiling causes a 30% performance loss. This statement is an oversimplified and incomplete understanding of the problem yet in many cases it is correct. Here is a bit more information to help understand the “PV soiling problem” a bit better. The graph above shows average daily PV soiling levels around the globe. Notice that the highest rates are 1.3% vs 30%. So why does the internet say 30% over and over again? In many cases, PV cleaning is identified as a need when performance levels have dropped 30% due to days or years without cleaning. The solar technician reads the inverter upon arrival and then again after cleaning. The 30% boost is accurate for that one specific project. However, a 30% performance loss may have taken 2 years, and soiling levels accumulated during this period. PV soiling levels can be measured “By Day” or over the year. The accumulated value sets off the cleaning event.
Another key thing is that PV soiling is site-specific. In the graph above, average daily soiling values per zone are demonstrated but 2 sites that are only 5 miles apart may have drastically different soiling levels. Why is this? One site may be next to a cement factory as we can see below, and one may be in an open meadow.
How Can Solar Panel Ceramic Coatings add Value?
Ceramic coatings vary significantly. There are 3 main categories. Each coating has its value. Understanding the main categories will help you identify which one to apply.
- Solar Protective Coatings
- Solar Easy-to-Clean Coatings
- Solar Self-Cleaning Coatings aka PV self-cleaning coatings
“So basically, depending on your problem, you should choose a different coating.”
Carla Dawson
Protective Hard Coatings | Easy-to-Clean Coating | PV Self-Cleaning Coating | |
Technical Specifications | |||
Hydrophobic | X | X | |
Hydrophilic | |||
Super Hydrophilic | X | ||
Alcohol Based | X | X | |
Water Based | X | ||
Ceramic Properties | X | X | |
Modular Matrix System | X | ||
“Hard Coatings” | X | ||
Logistics – Boat Freight | X | X | |
Logistics – Air Freight | X | ||
Protective Layer for Anti-Reflective Coatings | X | X | X |
Easy Cleaning – Less Effort – Less Time | X | X | X |
Restores glass to like-new condition | X | X | X |
Prevents stains, corrosion, and etching | X | X | X |
Keeps glass cleaner for longer | X | X | X |
Cuts cleaning time by up to 90% | X | X | X |
Eco-friendly; eliminates chemical cleaners | X | ||
PV Self-Cleaning Technology – Photocatalytic | X | ||
Brand Names – DiamonFusion | X (includes Ceramic properties) | ||
Brand Name – EnduroShield | X (No Ceramic properties) | ||
Brand Name – Elioxx.com | X (Includes Ceramic properties) | ||
Quality Lab Certifications | |||
Fraunhofer | X | ||
TUV Rheinland | X | ||
Intertek | X | ||
ISO | X | ||
Can PV Self-Cleaning Coatings be applied everywhere?
In general, PV self-cleaning coatings provide their full value where their humidity, and dew, and where there is infrequent or frequent rain.
Do Humidity Levels Affect the Soiling Problem?
Absolutely. The PV soiling problem varies significantly based on humidity levels. There are 3 main situations and the ideal solution varies significantly
In areas where there is a dry season and a wet season, photocatalytic ceramic coatings for solar panels add the following values
Areas with some Humidity
- They protect the anti-reflective coatings from natural degradation and help reserve that 3-4% boost
- They reduce PV soiling cementation levels by sealing the porous glass surface. The value added here is that the natural forces of dew, rain, water, and gravity can carry the dirt off leaving the surface clean without traditional solar panel cleaning systems that include water and brushes. In other words, coating with photocatalytic ceramic coatings designed for solar panels means you no longer have to clean with brushes and water in many situations. Why not all situations? Ceramic coatings cannot solve a “Cement factory nearby problem”. They can solve a standard PV soiling problem as long as the solar panels are not flat and have a pitch of 15 degrees or more and rain and or dew are constant. The northeast USA for example is an ideal area for photocatalytic ceramic coatings.
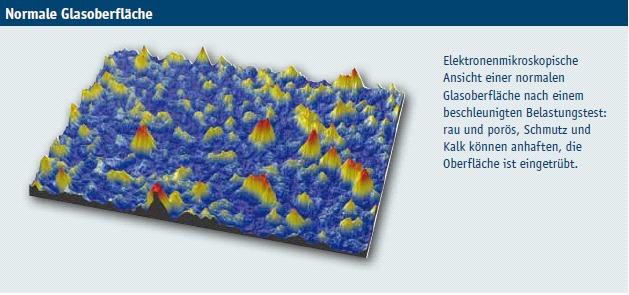
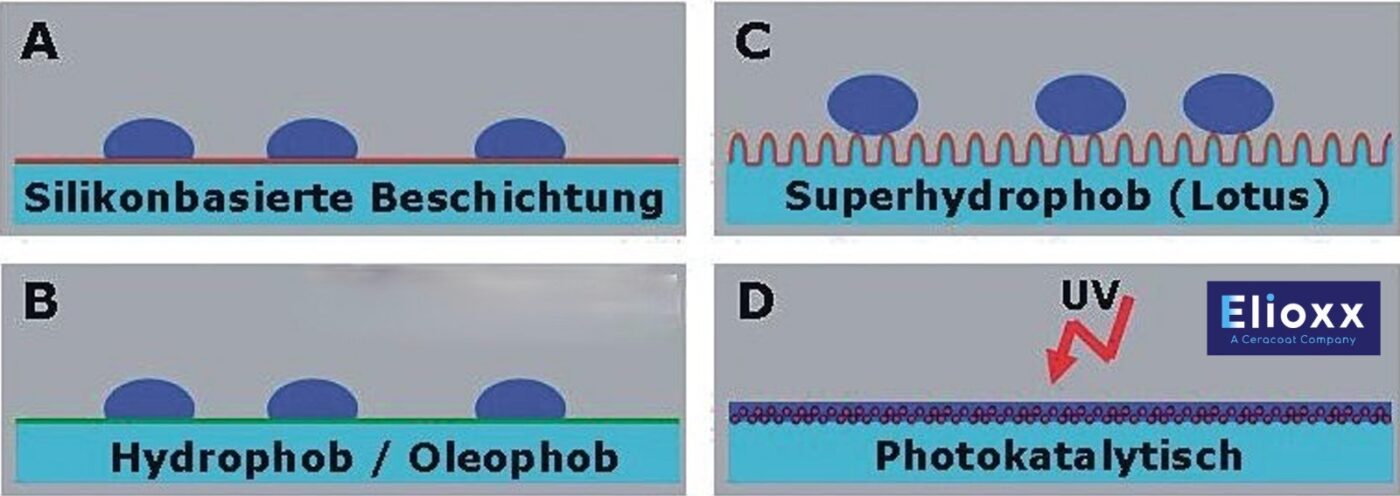
Area with lots of Humidity
In areas where rain is frequent, PV soiling is generally low. While the rain does not clean the panels, it helps. Here is another situation where the application of photocatalytic ceramic coatings for solar panels makes sense.
Area with 0 Humidity
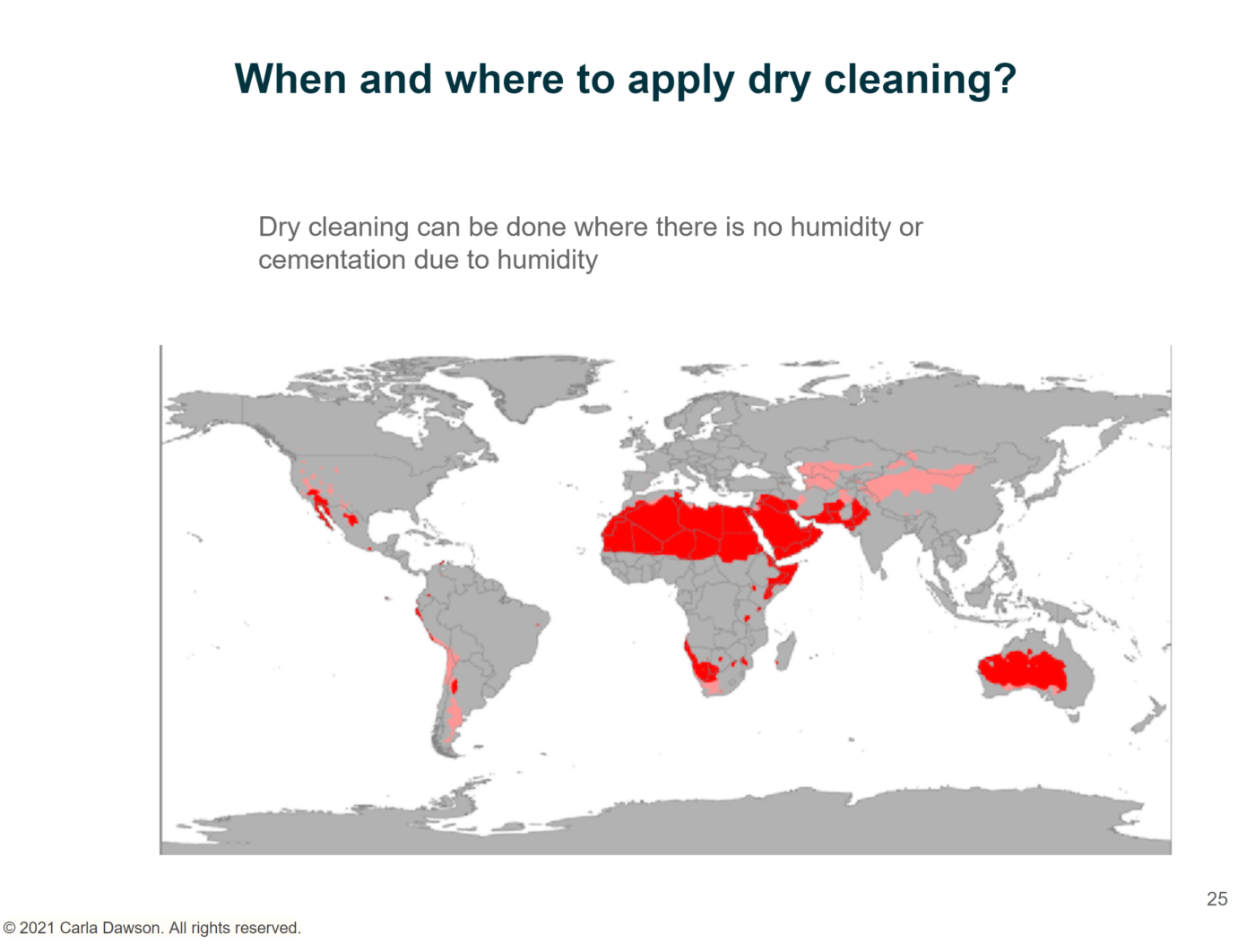
In areas where humidity levels are non-existent or very low, dry cleaning is the best solution. Ceramic coatings for solar panels add an “Easy Cleaning Value” and a “Protect the anti-reflective coatings value” but not a self-cleaning value.
There is a time and a place for robotic cleaning just like there is a time and place for using solar panel ceramic coatings. If you are interested in learning more, please feel free to sign up for our free 40-minute Calendly meetings here. calendly.com/soilar-tech/. We work worldwide.
Soilar Technologies is a PV soiling engineering company dedicated to improving solar assets bottom line safely.
Follow us on Instagram, Linkedin, Twitter.
Copyright © 2019 Carla Dawson. All rights reserved.
All documents are protected within the meaning of copyright law.
Carla Dawson reserves all rights to exercise intellectual property rights.
Copying of this content is not permitted without express written authority.
Violations are an offense and are liable for damages.
About the author

Carla Dawson founded Soilar Technologies, a NextGen PV Soiling Mitigation Technology Company in 2019.
NextGen PV soiling mitigation can be defined as:
“Mitigating photovoltaic soiling by using 21st-century technologies throughout the solar plant lifecycle with the objective of increasing performance, reliability, asset life, and warranty compliance. NextGen PV Soiling mitigation is typically a data-enriched smart system that combines technologies such as solar panel cleaning robotics, PV anti-soiling coatings, PV abrasion testing, bird deterrent solutions, PV soil monitoring, electrodynamic shields (EDS), condensation prevention, tracker/stowage position, and cleaning schedule optimization, solar panel cleaning software, analytics and other technologies.”
NextGen PV soiling mitigation is a phrase that was coined by Carla Dawson and Klemens Ilse in 2022.
Soilar Technologies is dedicated to helping solar panel cleaners, EPC, solar installation companies, and entrepreneurs solve their PV soiling problems from design to the operations and maintenance stage.